Well before the pandemic, many companies relying on Chinese producers for finished goods and parts were looking to de-risk by finding alternative suppliers in other countries. Why? Geopolitical tensions, trade disputes, and rising costs in China.
Trade tensions and national security concerns have led to a wave of legislation in the United States, where there are more than 60 bills pending in Congress aimed at changing economic relations with China. In addition, U.S. brands and manufacturers comparing China’s labor costs to those in Mexico have seen China’s labor costs rising faster. That has eroded China’s competitiveness and made Mexico more attractive.
Outward migration of production was underway before the pandemic because tariffs imposed by the U.S. and China had increased supply chain costs by up to 10% for as much as 40% of companies sourcing in China, according to Kamala Raman, a senior director analyst at Gartner.
The U.S., Germany, Japan and other countries have expressed strategic concerns about overreliance on China for critical products: 5G telecommunications gear, semiconductors, steel, cranes, electrical power equipment and more. McKinsey identified 180 different products for which one country — most often China — accounts for more than 70% of the global export market. Many of the products are chemicals and pharmaceuticals.
Intel recently divested itself of a business in politically sensitive memory chips because the business was heavily dependent on China sales. Samsung and others have cited cost considerations for production moves or asset sales.
The pandemic is turning concern to action
China’s assertive response to the pandemic included lengthy, mandatory lockdowns that froze manufacturing and stranded global cargo shipments for several weeks in the spring of 2020. That caused unprecedented disruption in supply chains and led to shortages of everything from household goods and consumer electronics to industrial components and healthcare products.
The pandemic exposed the fragility of sprawling global supply chains. In one recent survey, one-quarter of businesses sourcing from China indicated plans to transition all or some of their operations to other countries over the next three years. In a Gartner survey, an even higher percentage – 33% — said they intend to pull manufacturing or sourcing out of China in the next two to three years. Sixty-four percent of North American manufacturing and industrial professional said they were likely to bring manufacturing production and sourcing back to North America, in a Thomas Publishing survey.
It’s not just China
Supply chain risk has been rising for years as costly disruptions become regular occurrences.
McKinsey says weather disasters alone accounted for 40 separate incidents involving damage in excess of $1 billion in 2019. Add the risk from trade disputes, retaliatory tariffs — and a doubling of cyberattacks in a single year at a time when companies are increasing their reliance on digital systems.
Geopolitical risk is unavoidable. Today, 80% of trade involves countries with declining stability scores. “Companies can now expect supply chain disruptions lasting a month or longer to occur every 3.7 years, and the most severe events take a major financial toll,” McKinsey says.
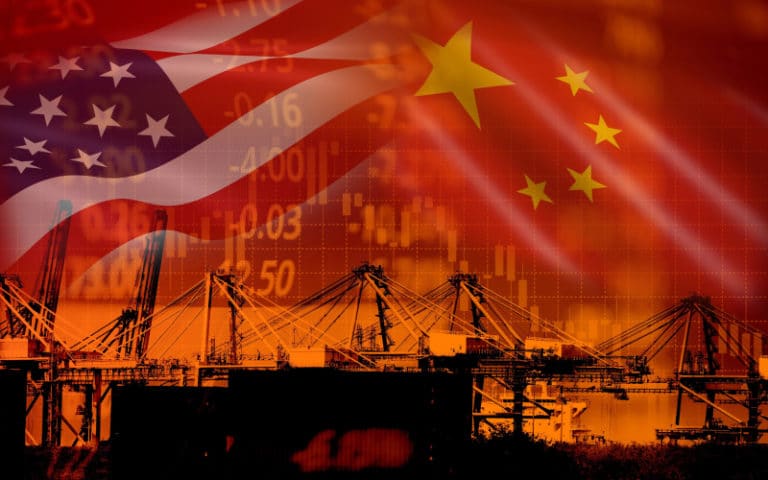